User:Tanganyingcao
![]() | This article includes a list of general references, but it lacks sufficient corresponding inline citations. (December 2017) |
Overview[edit]
- Transformers for power converters are distinctive from fundamental frequency high power power transformers, e.g. their air gaps not only determine inductance but also store energy for cycle-by-cycle charging-discharging.
- Electromagnetic interference issue will be discussed with a solution shielding technique provided.
Introduction[edit]
What is transformer? Transformer is a static electric device, which transforms electrical energy from one electrical circuit to another by means of common magnetic field and Faraday electromagnetic induction. For power systems, fundamental frequency operation and heat dissipation make the bulky size unavoidable.
Transformers in power converters[edit]
Operating at high frequency and supplying low power, power converters have much smaller transformers as compared with those of fundamental frequency, high power applications.
Why use transformers in power converters[edit]
Transformers are used in power converters to incorporate:
a. Electrical isolation;
b. Voltage step-down.
The secondary circuit is floating, when you touch the secondary circuit, you merely drag its poential to your body potential or the earth potential. There will be no current flowing through your body. That's why you can use your cellphone safely when it is being charged, even if your cellphone has a mental shell and it is connected to the secondary circuit.
Usually, in power systems, transformers transmit power simultaneously, no charge!
The current in the primary winding of a transformer plays two roles:
1. It sets up the mutual flux in accordance with Ampere’s law.
2. It balances the demagnetizing effect of the load current in the secondary winding.
The net MMF is and, in terms of the magnetic circuit law, this may be related to the reluctance of the transformer core
Thus, the primary current has two components: the magnetizing component and a load component reflected into the primary
Flyback converter’s transformer works differently, like an inductor. In each cycle, flyback converter’s transformer first gets charged then releases its energy to the load.
Flyback converter’s transformer air gap has two functions. It not only determines inductance, but also stores energy. For flyback converter, the transformer gap can have the function of energy transmission through cycles of charging and discharging.
Core’s relative permeability can be >1, 000, even >10, 000. While the air gap features much lower permeability, accordingly has higher energy density.
Electromagnetic interference issue and solution[edit]
Noise propagation through earth is an annoying problem, especially for communication, which should be reduced.
Transformer is critical for CM noise generation in isolated power converters. CM noise suppression needs to be considered in transformer design as early as possible.
CM noise suppression solution: secondary litz wire shielded[edit]
Equal potential will induce zero displacement current, thereby zero CM noise. To enclose the litz wire with a copper foil is to form an equal potential distribution along the inner core wire.Then the inner core wire and outer shielding has the same potential, resulting in zero displace current, zero CM noise.
Litz wire shielded secondary winding can share the advantage of the bifilar structure, as of reduced CM voltage conversion ratio through wide frequency range. Capacitive coupling to litz wire shielding will be confined to the primary loop, with no CM contribution. The shielding will behaves like a wall, blocking the electric coupling from primary windings and aux winding to the enclosed secondary winding.
With this technique, CM noise through low frequency (<2MHz) could be reduced, with margin improved from 0dB to 11dB. Thereby cumbersome CM inductor for low frequency noise suppression can be removed. Adapter can be smaller.
Real Wikipedia Page[edit]
Wikipedia, “Core Gapped Transformers for Power Converters,” Online, 2017. https://en.wikipedia.org/wiki/Nuclear_magnetic_resonance
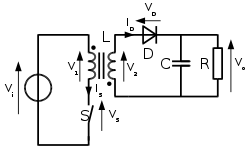
The flyback converter is used in both AC/DC and DC/DC conversion with galvanic isolation between the input and any outputs. The flyback converter is a buck-boost converter with the inductor split to form a transformer, so that the voltage ratios are multiplied with an additional advantage of isolation. When driving for example a plasma lamp or a voltage multiplier the rectifying diode of the boost converter is left out and the device is called a flyback transformer.
Structure and principle[edit]


The schematic of a flyback converter can be seen in Fig. 1. It is equivalent to that of a buck-boost converter,[1] with the inductor split to form a transformer. Therefore, the operating principle of both converters is very similar:
- When the switch is closed (top of Fig. 2), the primary of the transformer is directly connected to the input voltage source. The primary current and magnetic flux in the transformer increases, storing energy in the transformer. The voltage induced in the secondary winding is negative, so the diode is reverse-biased (i.e., blocked). The output capacitor supplies energy to the output load.
- When the switch is opened (bottom of Fig. 2), the primary current and magnetic flux drops. The secondary voltage is positive, forward-biasing the diode, allowing current to flow from the transformer. The energy from the transformer core recharges the capacitor and supplies the load.
The operation of storing energy in the transformer before transferring to the output of the converter allows the topology to easily generate multiple outputs with little additional circuitry, although the output voltages have to be able to match each other through the turns ratio. Also there is a need for a controlling rail which has to be loaded before load is applied to the uncontrolled rails, this is to allow the PWM to open up and supply enough energy to the transformer.
Operations[edit]
The flyback converter is an isolated power converter. The two prevailing control schemes are voltage mode control and current mode control (in the majority of cases current mode control needs to be dominant for stability during operation). Both require a signal related to the output voltage. There are three common ways to generate this voltage. The first is to use an optocoupler on the secondary circuitry to send a signal to the controller. The second is to wind a separate winding on the coil and rely on the cross regulation of the design. The third consists of sampling the voltage amplitude on the primary side, during the discharge, referenced to the standing primary DC voltage.
The first technique involving an optocoupler has been used to obtain tight voltage and current regulation, whereas the second approach has been developed for cost-sensitive applications where the output does not need to be as tightly controlled, but up to 11 components including the optocoupler could be eliminated from the overall design. Also, in applications where reliability is critical, optocouplers can be detrimental to the MTBF (Mean Time Between Failure) calculations. The third technique, primary-side sensing, can be as accurate as the first and more economical than the second, yet requires a minimum load so that the discharge-event keeps occurring, providing the opportunities to sample the 1:N secondary voltage at the primary winding (during Tdischarge, as per Fig3).
A variation in primary-side sensing technology is where the output voltage and current are regulated by monitoring the waveforms in the auxiliary winding used to power the control IC itself, which have improved the accuracy of both voltage and current regulation. The auxiliary primary winding is used in the same discharge phase as the remaining secondaries, but it builds a rectified voltage referenced commonly with the primary DC, hence considered on the primary side.
Previously, a measurement was taken across the whole of the flyback waveform which led to error, but it was realized that measurements at the so-called knee point (when the secondary current is zero, see Fig. 3) allow for a much more accurate measurement of what is happening on the secondary side. This topology is now replacing ringing choke converters (RCCs) in applications such as mobile phone chargers.
Limitations[edit]
Continuous mode has the following disadvantages, which complicate the control of the converter:
- The voltage feedback loop requires a lower bandwidth due to a right half plane zero in the response of the converter.
- The current feedback loop used in current mode control needs slope compensation in cases where the duty cycle is above 50%.
- The power switches are now turning on with positive current flow - this means that in addition to turn-off speed, the switch turn-on speed is also important for efficiency and reducing waste heat in the switching element.
Discontinuous mode has the following disadvantages, which limit the efficiency of the converter:
- High RMS and peak currents in the design
- High flux excursions in the inductor
Applications[edit]
- Low-power switch-mode power supplies (cell phone charger, standby power supply in PCs)
- Low-cost multiple-output power supplies (e.g., main PC supplies <250 W [citation needed])
- High voltage supply for the CRT in TVs and monitors (the flyback converter is often combined with the horizontal deflection drive)
- High voltage generation (e.g., for xenon flash lamps, lasers, copiers, etc.)
- Isolated gate driver
See also[edit]
- Forward converter
- Joule thief - Minimalist switchmode converter example
References[edit]
- Billings, Keith (1999), Switchmode Power Supply Handbook (Second ed.), McGraw-Hill, ISBN 0-07-006719-8

- ^ The Flyback Converter - Lecture notes - ECEN4517 - Department of Electrical and Computer Engineering - University of Colorado, Boulder.
[[Category:Electric power conversion]]